①設計主導のコストダウン 新規設計を出来るだけ行わない
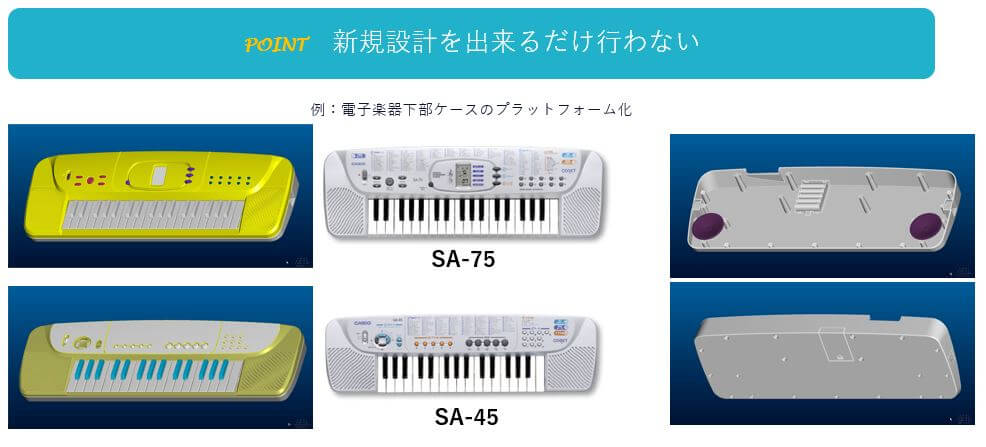
プラットフォーム化の具体例として、電子楽器を例に説明します。
機種に関わらず、鍵盤は構造も比較的簡単な事から、有る程度共通化されて長く流用設計されて来ました。
ほとんどのキーボードモデルの基本構造は上下部のケースで構成されていますが、下部ケースはプラットフォーム化されて機種間で流用されています。
つまり下部ケースは数年に一度、或いは長期間流用され、機種変更では、上部ケースのみ金型を起工して変更しています。
①設計主導のコストダウン 出来るだけ部品を流用する
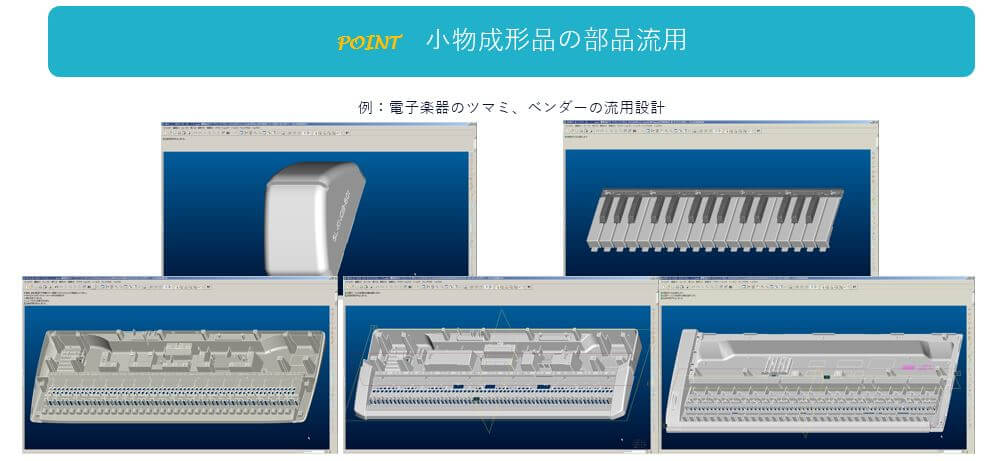
部品流用の具体例として、やはり電子楽器を例に説明します。
電子楽器の製品構成では、ツマミ、ノブなど、比較的小さい部品もありますが、金型を起工する必要があります。
ツマミ等は、事業部からデザイナーに対して極力流用を依頼していますが、流用する事で原価削減となりコストダウン効果は大きいです。
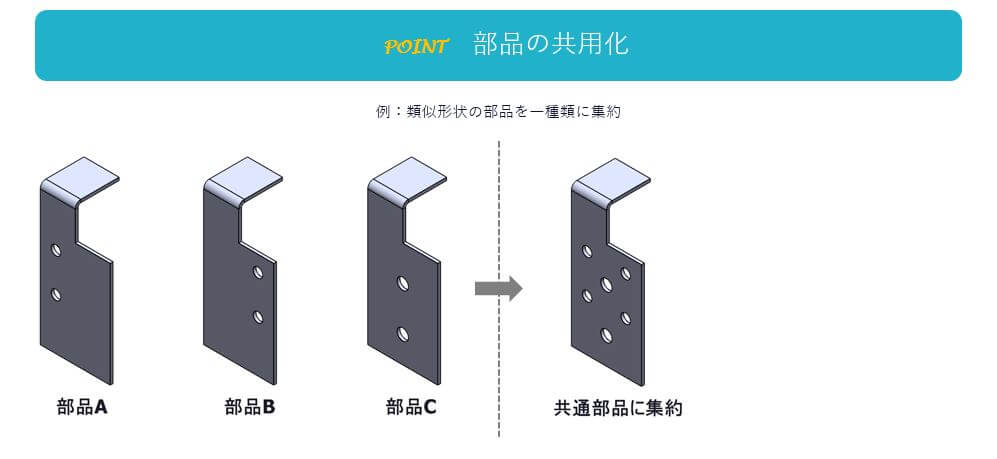
同形状で穴の位置が異なるものなどであれば、上図のように1 つの共通部品に集約することも可能です。
別々の部品を1 つの部品としてまとめて生産できるため、部品自体の短納期の実現や、部品自体のコストダウンも実現することができます。
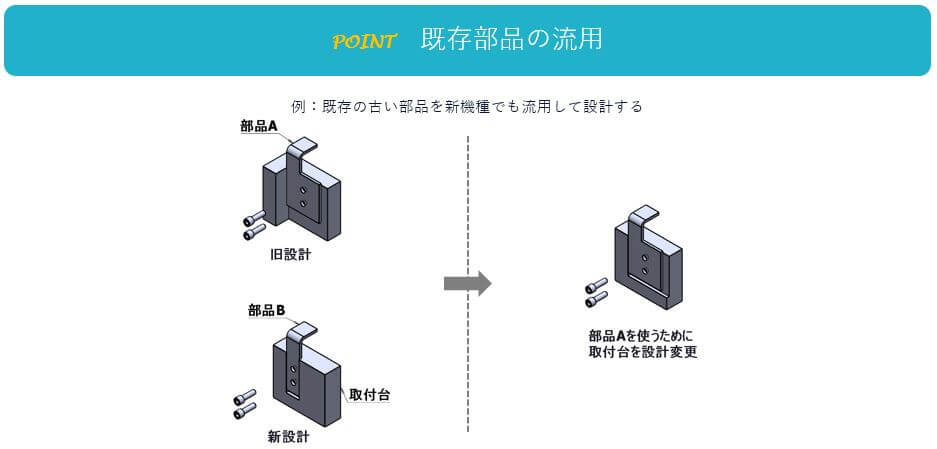
変更設計ではなく新規設計を行う場合、共用として指定されていない場合、どうしても部品を全て新しく設計しがちです。
ですが、既に生産している部品が使える場合もあり、流用部品を使うか、新規部品になるかは、設計次第になります。
古い部品を流用するメリットは、協力会社との納入単価調整で同じ部品を新規設計するより安い場合がある。
部品生産数量が増えれば、部品単価がさらに下がる可能性が有るので、部品自体のコストダウンも実現することができます。
①設計主導のコストダウン 設計手順や考え方を統一する
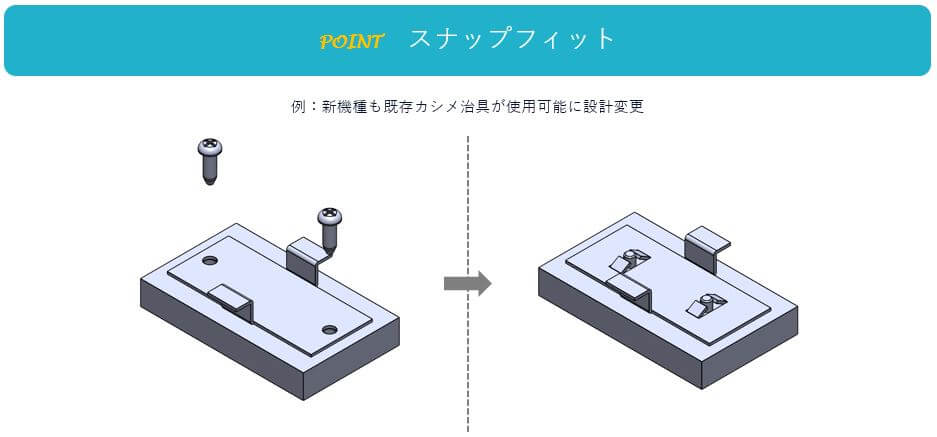
板金においてコストダウンをするには、溶接をせず、かつ部品をできるだけ一体化曲げのみで形状を作ることができないかを検討することが重要です。
板金と成形をくっつける
・ネジを使わずに止められる
(リモコンってネジがなくて、ハマっている)

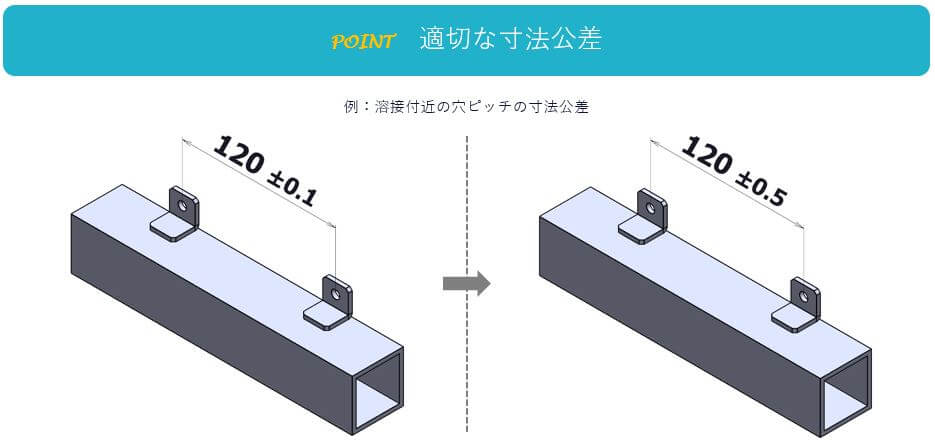
溶接する場合には、溶接時の熱によって発生する歪みや収縮を考慮し設計を行い、寸法公差を入れる必要があります。
溶接で組み合わせた部材の穴ピッチに厳しい寸法公差が入っている場合、溶接の熱により発生する歪みや収縮の為、修正や矯正を行うコストがかかります。
或いは、溶接後に後加工を行う必要が有ります。
穴ピッチの公差が有る程度の寸法公差まで緩和できれば、簡単な治具で位置決めして溶接加工で対応することができます。
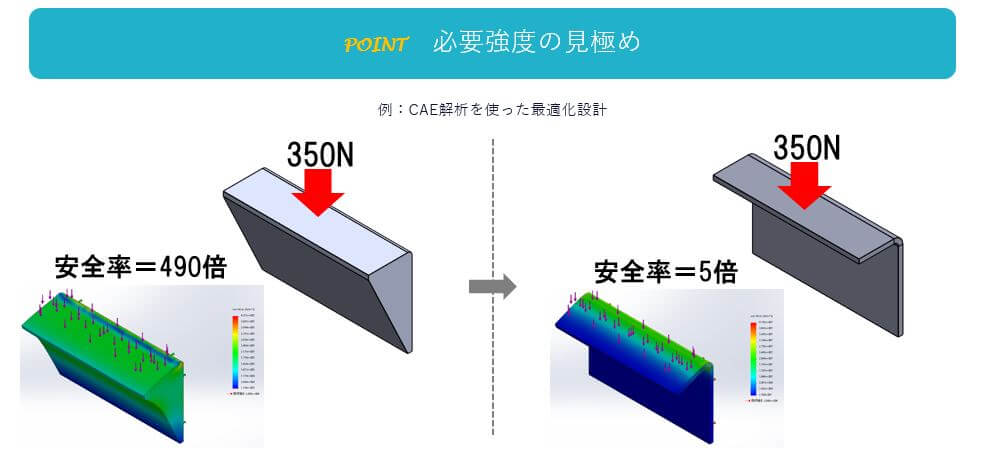
強度部材の設計では、部材に掛かる強度を考慮して部材、形状を検討します。
手計算で必要強度から決定して行く方法も有りますが、簡単なモデルを作成し、 CAE解析で強度を見ながら形状の最適化設計を行う事で、材料費を削減することが可能です。
①設計主導のコストダウン 設計でコスト検証を行う

機械加工の場合
以前は、標準的な外注加工費や、コストの掛かる形状などをリスト化して、設計担当にコスト意識を持たせていた。
現在は、ミスミなどで3Dデータから簡単に見積が取れるので、設計段階の形状検討で費用概算が出せる。
樹脂成形の場合
樹脂成形の単価は成形費用は比較的明確なので、カシオの楽器設計ではエクセルの簡易計算で算出していた。